The importance of batch-to-batch consistency
The fundamental decision that all new MIM part producers have to make is whether to purchase feedstock from a specialist supplier, or whether to develop and manufacture it in-house. There is no right or wrong decision here, as both choices have advantages and disadvantages.
For some of the longest established producers, there was no choice. No feedstock suppliers existed in the early days of Metal Injection Molding, so you either had to acquire a licence or try and develop a binder system yourself. Today there is a good choice of ready-to-mould feedstock suppliers who offer a diverse range of off-the-shelf feedstock, as well as custom materials.
One of the many secrets to successful Metal Injection Molding production is, however, to have absolute batch-to-batch consistency in your feedstock. If this is not achieved, then defects can occur in moulding, as well as distortion in sintering.
For those who wish to manufacture their own feedstock in-house, binder systems know-how is available. There are a number of technologies used to mix and compound powders and binder constituents to produce Metal Injection Moulding feedstock.
Sigma blade kneaders
Compounding involves exerting, at the same time, heat and shear on the material. A frequently used apparatus is the heated kneader with sigma or Z shaped blades. Kneaders with a discharging screw allow the extrusion of the feedstock and shred it into more or less regular pellets.
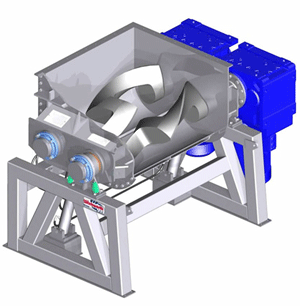
Fig. 9 A typical z-blade mixer for Metal Injection Molding feedstock production. (Image Courtesy Winkworth Mixers, UK)
Kneading is a batch type process and kneaders of various sizes are available, even very small ones for batch sizes of less than 1 kg. Therefore the process can be downscaled to laboratory requirements, which was an advantage in the development phase of MIM technology.
Kneaders can, however, tend to have dead corners where little or no shear is exerted and, for the industrial production of larger quantities of feedstock, other methods appear to be more efficient.
Twin screw and shear roll extruders
The twin screw extruder is a very efficient compounding device with a high throughput. Various screw geometries are in use. The system works in a similar way to the plastifying unit of an injection moulding machine.
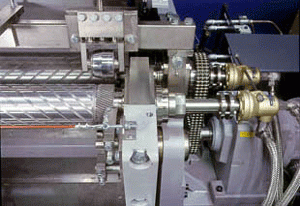
Fig. 10 A shear roll extruder used in the higher volume production of Metal Injection Molding feedstock. (Image courtesy Bellaform GmbH, Germany)
The raw material is intensively sheared and transported forward in a heated barrel by two screws. At the end, it is extruded and can then be pelletised. The process is continuous and allows the production of large quantities in a single production run.
A relatively new compounding technology is shear roll extrusion. Two parallel heated rolls with helical grooves are rotated and the powder-binder mix is fed on one roll. The slot between the rolls can be adjusted. It is usually 5 to 7 mm wide, so that the entire mass is forced into the grooves.
The driving roll is rotated a little faster than the roll carrying the feedstock to increase the shear intensity. Due to the groove geometry, the mass is transported towards the outlet at the end where it is extruded and shredded by a rotating wheel.