Alloy options
A wide variety of alloys are available in the MIM grade particle sizes. The bulk of the materials fall into a few categories:
-
Ferrous alloys: steels, stainless steels, tool steels, iron-nickel magnetic alloys, and speciality ferrous alloys such as Invar and Kovar
-
Tungsten alloys: both tungsten heavy alloys and tungsten-copper
-
Hard materials: cobalt-chromium, cemented carbides (WC-Co), and cermets (Fe-TiC)
-
Special materials that include aluminum, precious metals, titanium alloys, nickel, nickel-base superalloys, molybdenum, molybdenum-copper, and particulate composites.
Most of the alloys are copies from standard handbook formulations. However, the long-term anneal associated with sintering degrades properties, since most of the alloys were developed in the context of casting technologies. Thus, modified chemistries are emerging that are customised to MIM technology.
For example, the 316L composition (Fe-19Cr-9Ni-2Mo) is used because of its combined strength and corrosion resistance. Compositions with extra chromium ease sintering. Although more expensive, such alloys provide properties superior to that attainable via alternative metal working approaches.
Custom powders can be fabricated when a composition is not available, but at an additional cost. With many vendors of small powders, undoubtedly almost any material can be custom fabricated for MIM, if the price is right. Powder cost impacts final component cost so it is best to use one of the several common alloys.
Properties
Since MIM products are usually sintered to about 98% density, the densities are slightly below theoretical, similar to a casting. Accordingly, the chemical, physical, elastic, electrical, and thermodynamic attributes match the values found in handbooks. For example, Table 2 shows thermal typical properties of MIM materials used in electronic systems.
MIM testing has emphasised mechanical properties. When sintered, the tensile properties usually match those obtained using other manufacturing routes [3].
Surgical stainless steel with the 17-4 PH composition (AISI 630) is one of the most widely used MIM alloys. It consists of iron with 17% Cr, 4% Ni, 4% Cu, and low contents of Mn, Si, and Nb or Ta. When sintered and heat treated to the H1025 condition, the MIM product typically has a yield strength of 980 MPa, but ranges between vendors from a low of 965 MPa to a high of 1040 MPa. However, the sintering step used in MIM does induce a coarse grained microstructure that tends to show up in a lower ductility and tensile strength.
In one study [3], the yield strength was superior by MIM, but 50% of the MIM samples (from a test lot of 50) fell below the 1070 MPa handbook tensile strength. This is because the residual pores in the MIM material induced premature fracture during the tensile test, giving less plastic flow (elongation) prior to failure. Table 3 is only representative of the properties attainable in MIM, since differences in impurity levels, grain size, porosity, and post-sintering heat treatment can have dramatic effects.
Fatigue strength and fracture toughness
Sometimes a problem is evident in the dynamic properties such as fatigue strength or fracture toughness. For high toughness materials this is not an issue. But in other cases testing is recommended. For the 17-4 PH surgical stainless steel, V-notched impact tests showed the MIM material had only 15% of the fracture energy of wrought (even when the wrought material was subjected to the same sintering thermal cycle) [4]. The fatigue strength for MIM 17-4 PH stainless steel at 10 million cycles is 500 MPa. This is slightly lower than the cast or wrought product and reflects the larger grain size and residual porosity associated with MIM.
Corrosion resistance
Corrosion resistance of MIM stainless steels can be a problem. The high vapour pressure of chromium when compared to nickel and iron leads to preferential surface evaporation of the chromium during sintering, which degrades resistance to corrosion attack. One consequence is deep pitting corrosion in areas devoid of the proper chromium content, such as seen in Fig. 10.
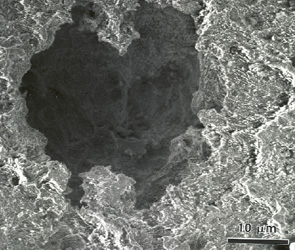
Fig. 10 Corrosion pitting in a MIM 17-4 PH stainless steel that was not properly treated to homogenise the chromium distribution after sintering. This problem can be avoided by post-sintering thermal, chemical, or mechanical treatments
Actual corrosion behaviour depends on the MIM processing conditions and the test conditions. Collins [5] tested several MIM vendors versus wrought material and concluded ‘… the performance of the MIM materials was inferior to wrought in the pitting corrosion tests…’. She found that as the surface roughness decreased (due to post-sintering polishing) the corrosion resistance improved. Thus, with proper post-sintering processing and surface treatment she concluded MIM 316L stainless steel can perform as well as wrought in general corrosion resistance to a variety of media.
Biocompatibility
As MIM moves into more medical and dental applications, the presumption has been that biocompatibility will be equivalent to other routes. A few tests with titanium and stainless steels have shown this is not the case. Accordingly, caution is appropriate since sintering degrades the surface chemistry and post-sintering polishing or electrochemical treatments are required to re-establish the uniform surface chemistry required for biocompatibility. In artificial saliva tests MIM 17-4 PH exhibits pitting corrosion if it was not polished first.
Opportunities for improving wear performance
Wear testing shows MIM has a significant opportunity, since hard phases can be mixed into the feedstock to improve behaviour. For example, MIM tool steels treated with a low concentration of calcium difluoride delivers a 30-fold decrease in dry wear rate versus wrought tool steel [6].
Other dramatic improvements in wear resistance are seen by adding titanium nitride or chromium boride to stainless steels; products that cannot be formed using traditional metalworking practices.
Material | Density g/cm³ | Tensile Strength Mpa | Elastic Modulus Gpa | Thermal Conductivity W/(m K) | Thermal Expansion 10-6/k |
Aluminum (Al) | 2.7 | 100 | 70 | 180 | 23 |
Copper (Cu) | 8.9 | 100 | 130 | 250 | 13 |
Invar (Fe-36ni) | 8 | 300 | 205 | 20 | 5 |
Kovar Or F15 (Fe-29ni-17co) | 8 | 480 | 200 | 17 | 4.9 |
Molybdenum-copper (Mo-15cu) | 10 | 210 | 280 | 170 | 7 |
Molybdenum-copper (Mo-20cu) | 9.9 | 200 | 280 | 145 | 6.5 |
Tungsten-copper (W-10cu) | 17 | 500 | 340 | 209 | 6 |
Tungsten-copper (W-20cu) | 16 | 560 | 290 | 247 | 7 |
Tungsten-copper (W-30cu) | 14 | 420 | 260 | 260 | 11 |
Table 2 Properties of MIM thermal management alloys